你有没有遇到过这种情况——新买的手机壳用不了几天就开始脱胶,刚喷好的汽车漆面莫名其妙出现斑驳,或者医疗器械的涂层总是粘不牢?这些问题八成都是表面附着力不足惹的祸。在工业生产中,材料表面的附着力直接决定了产品质量和使用寿命,而真空等离子清洗技术正在成为解决这个痛点的秘密武器。
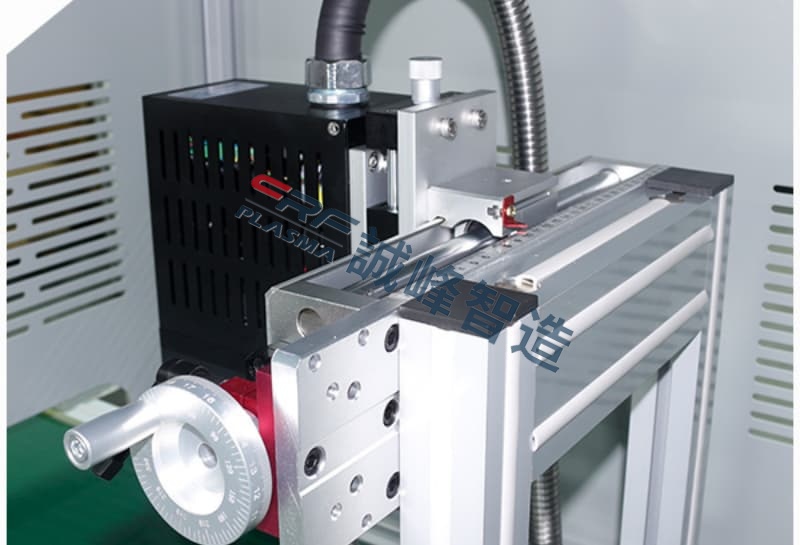
真空等离子清洗到底是什么黑科技
想象一下用看不见的粒子给材料表面做深度SPA,这就是等离子清洗的工作原理。在真空环境下,通过高频电场将气体电离成等离子体,这些活性粒子就像无数把小刷子,能精准清除材料表面的有机污染物和氧化物。更厉害的是,它还能在微观层面刻蚀出纳米级凹坑,让表面积增大数十倍。深圳诚峰智造的实验数据显示,经过等离子处理的金属表面,其附着力指标平均能提升2-3倍,某些高分子材料甚至能达到5倍以上的增幅。
为什么传统清洗方式总差点意思
拿最常见的超声波清洗来说,虽然能去除肉眼可见的油污,但对分子级的污染物束手无策。喷砂处理又容易损伤基材,化学清洗则可能留下残留物。相比之下,等离子清洗能在常温下作业,不会改变材料本体性能,处理后的表面就像新铺的柏油马路,涂料、胶水这些"车辆"自然跑得更稳当。有个做汽车配件的客户就发现,同样的喷涂工艺,经过等离子处理的零件在盐雾测试中寿命延长了400小时。
不同材料要选对处理模式
金属件适合用氩气等离子体,它能轰击出理想的粗糙度;塑料制品则要用氧气等离子,既能清洁又能引入极性基团。处理时间也很有讲究,像硅胶这类敏感材料,20秒足矣,而陶瓷可能需要3-5分钟。有家医疗器械厂商曾反映涂层总脱落,后来发现是没根据材料特性调整参数,改用氮气等离子体并控制功率在300W后,产品合格率直接从65%飙到98%。
生产线上这些坑千万别踩
见过有工厂把清洗舱当储物柜用,结果真空泵进了粉尘直接报废。还有操作员为省时间跳过预清洗,导致处理效果大打折扣。正确的做法是定期检查电极损耗,每批材料都做接触角测试。建议在流水线设计时就预留检测工位,像我们给某电子厂做的方案里,就集成了在线监测系统,发现问题能自动调整工艺参数。
未来这技术还能玩出什么花样
现在已经有实验室在研发大气压等离子技术,说不定哪天就能告别真空环境。智能控制系统也在升级,通过光谱分析实时调节处理强度。更让人期待的是复合处理技术,比如等离子清洗后立即进行原子层沉积,这对航空航天领域的高端零部件制造简直是福音。下次当你看到某款产品特别经久耐用时,说不定里面就藏着等离子处理的功劳。