最近和几个家电厂的技术主管聊天,发现不少企业还在用老办法处理塑料件表面。酒精擦、火焰烧、打磨抛光的场景在车间里随处可见,但说到大气等离子处理技术,很多人第一反应还是"太贵用不起"。这让我想起五年前智能手机刚开始用屏下指纹时,也有厂商觉得成本高,现在回头看,那些早早布局的厂家反而吃到了技术红利。
大气等离子处理究竟贵不贵
先算笔明白账。传统塑料件前处理要经过除油、粗化、水洗多道工序,光人工成本就占了大头。某家电企业做过对比,处理1平方米ABS塑料,传统工艺综合成本约3.2元,而大气等离子设备处理同样面积只要0.8元。这还没算废水处理费用和因表面不合格导致的返工损失。深圳有家做等离子清洗机的厂家透露,他们的客户通常在8-14个月就能收回设备投资,之后每处理一个零件都是在省钱。
为什么处理过的塑料更"吃漆"
等离子体里的活性粒子就像微观世界的小铲子,能在不损伤材料的前提下,把塑料表面刻蚀出纳米级的凹凸结构。这种变化肉眼看不见,但喷漆时油漆分子会牢牢卡在这些缝隙里。实验数据显示,经过等离子处理的PP材料,其涂层附着力能从原来的1级提升到4-5级(划格法测试)。家电行业的朋友应该清楚,这相当于把掉漆投诉率直接降了个数量级。
长期账本里藏着的惊喜
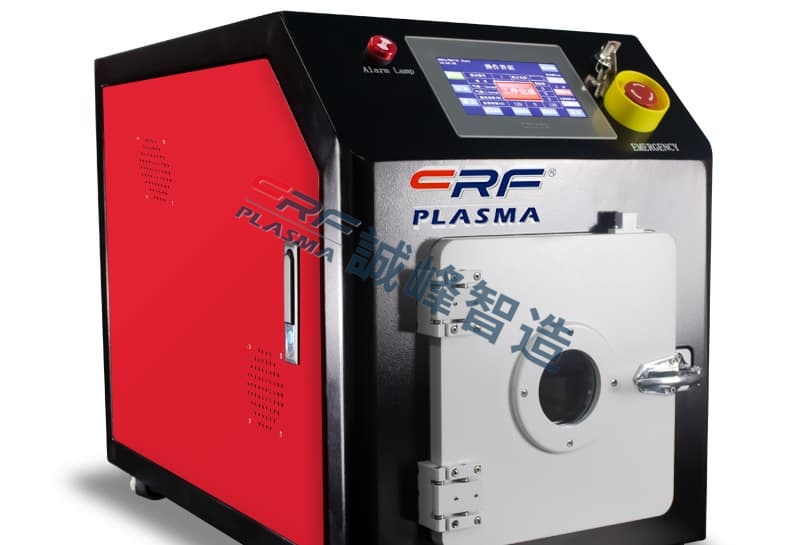
佛山某电饭煲代工厂的案例很有意思。他们去年在喷涂线上加装等离子设备后,最意外的收获是喷漆用量减少了18%。由于表面能提升,油漆流动性和覆盖性变好,同样效果可以用更薄的涂层实现。更关键的是产品耐久性变化,经过两年市场跟踪,处理过的面板按键区域几乎没出现漆膜脱落,售后维修成本直降40%。这种隐形成本节约,往往要使用一两年后才能真切感受到。
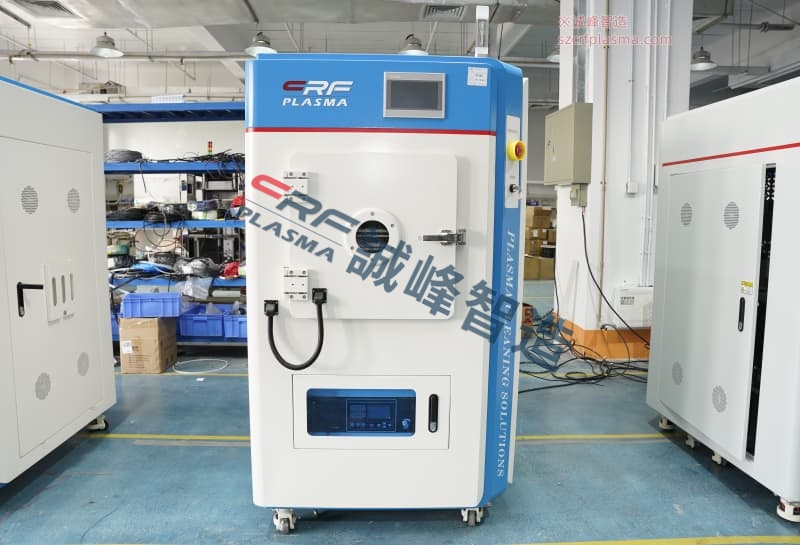
小批量生产也能玩得转
很多人以为这种设备只适合大型家电厂,其实现在模块化设计的等离子处理机已经能灵活适配不同产能。有个给扫地机器人做配件的供应商,他们每天就处理两三批塑料件,选择租赁方式使用设备,按处理面积计费,折算下来单件成本反而比外包化学处理还低15%。这种轻资产模式特别适合中小厂商技术升级,既不用一次性大投入,又能随时用上先进工艺。
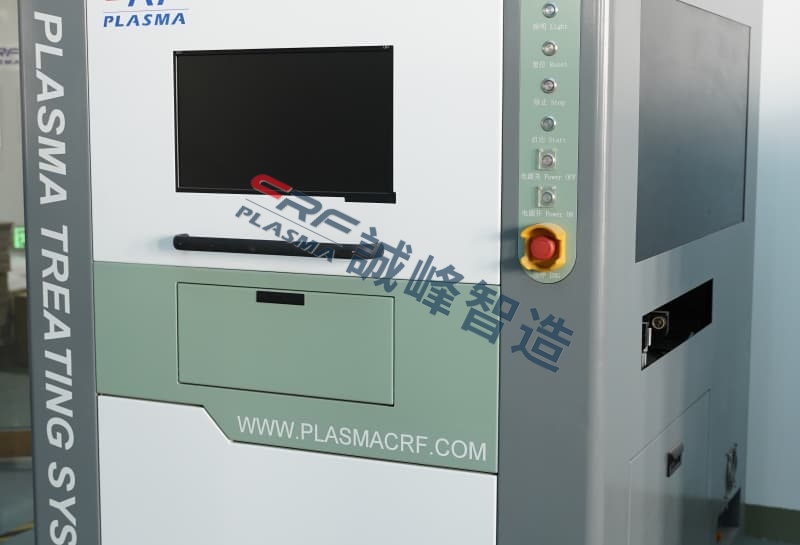
站在行业观察者的角度,塑料表面处理技术正在经历从化学方法向物理方法的转型。就像当年LED替代荧光灯管,早期投入看似增加,但算通整个产品生命周期的总账,反而是更经济的选择。那些还在用溶剂擦拭塑料件的企业,或许该重新拨拨算盘珠子了。