说到现代半导体制造,等离子处理室绝对是核心设备之一。就像炒菜离不开锅一样,芯片制造过程中几乎每个关键步骤都要用到这种设备。但你可能不知道,这些处理室内部有一层看不见的"防护服"——防沉积涂层,它就像是给处理室穿上的智能盔甲,既要保护设备不被腐蚀,又要确保工艺稳定运行。这层涂层的技术发展,其实藏着很多有趣的故事。
早期的等离子处理室面临的最大难题就是颗粒污染。那时候的涂层技术比较原始,主要采用简单的氧化铝涂层。这种材料虽然便宜,但在高频等离子体轰击下很容易剥落。想象一下,就像在暴风雨中打伞,劣质伞布没几下就被吹翻了。剥落的涂层碎片掉在晶圆上,直接导致整批产品报废。当时半导体厂最头疼的就是这个问题,经常要停机清理反应室,生产效率大打折扣。
进入21世纪后,碳化硅涂层开始崭露头角。这种材料的硬度是氧化铝的两倍多,耐等离子体腐蚀性能也大幅提升。就像给处理室换上了防弹衣,使用寿命明显延长。不过碳化硅也有软肋——它对某些特殊工艺气体的抵抗能力不够强。特别是在蚀刻工艺中,氟基气体很容易在碳化硅表面形成蚀坑。这时候工程师们想出了新办法,在碳化硅表面再镀一层特殊保护膜,就像给防弹衣外面又加了层雨衣。
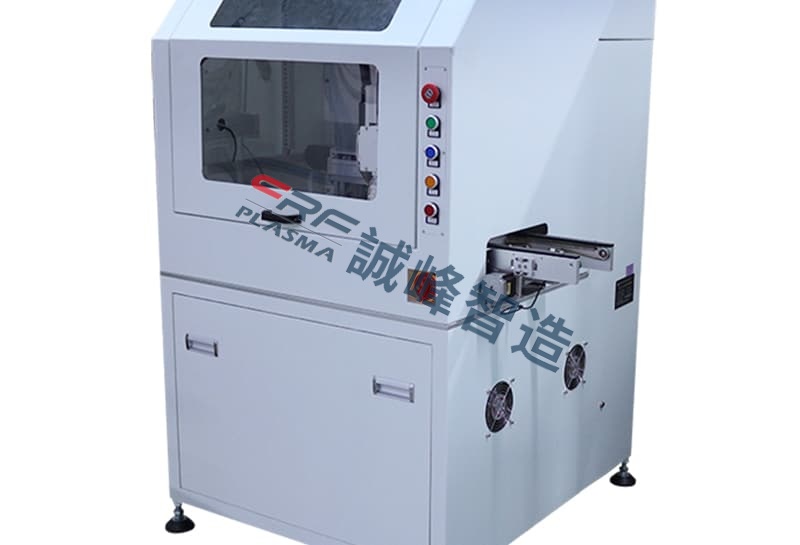
最近十年,复合涂层技术成为主流。现在的先进涂层都是"千层饼"结构,不同材料层层叠加,每层都有特定功能。最底层负责粘接,中间层承担主要防护,最外层则针对特定工艺优化。比如有些涂层会在表面设计纳米级凹凸结构,就像荷叶表面那样,让沉积物难以附着。这种设计思路的转变,标志着涂层技术从被动防护转向了主动防御。
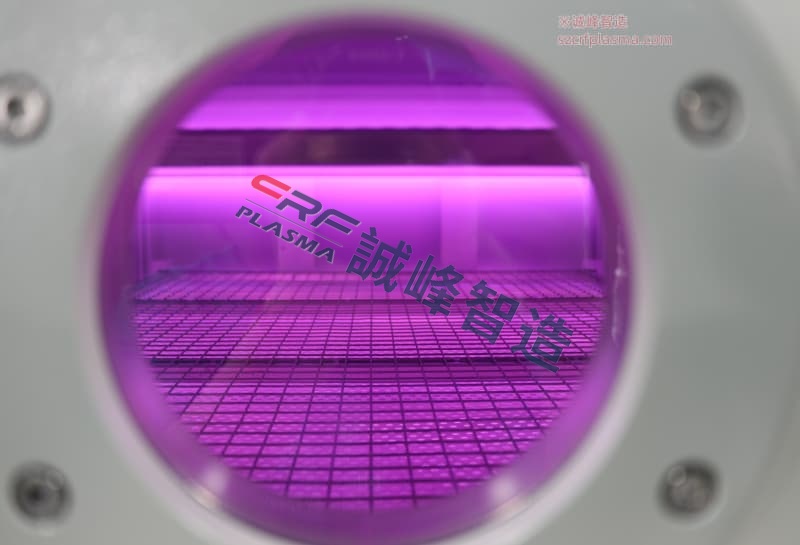
未来涂层技术可能会更加智能化。研究人员正在开发能自动修复的涂层材料,当表面出现微小损伤时,材料中的活性成分会自动填补缺陷。还有些实验室在研究具有传感功能的涂层,能够实时监测处理室内的状态变化。这些创新一旦实现商业化,将彻底改变半导体设备的维护模式。
在深圳,像诚峰智造这样的企业正在积极参与这场技术革命。他们研发的新型复合涂层已经在多家晶圆厂得到验证,帮助客户将设备维护周期延长了30%以上。不过要真正突破技术瓶颈,还需要整个产业链的共同努力。毕竟在纳米尺度上做文章,任何细微的进步都需要付出巨大努力。
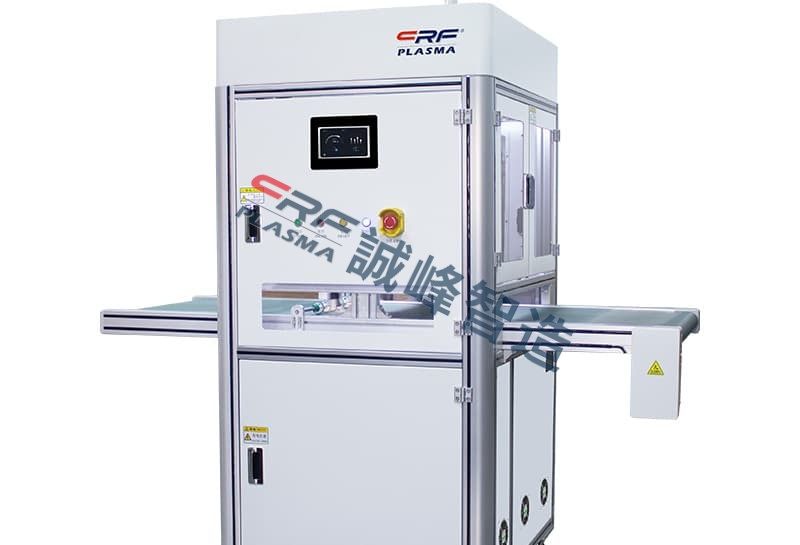
从最初的简单防护到现在多功能复合涂层,防沉积技术的发展历程就像一部微缩的半导体进化史。每次材料革新都伴随着工艺突破,而每个技术瓶颈的突破又推动着整个行业向前迈进。或许在不远的将来,我们今天认为不可能实现的涂层技术,会成为半导体车间的标配。